 |
Rare-Earth
Metals
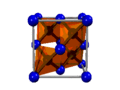
H2 |
Introduction
Currently, permanent magnets made from Nd2Fe14B type
alloys possess the best magnetic properties with maximum magnetic energies (BH)max
reaching up to 50 MGOe (400 kJ/m3) and extremal values of coercive
force and remanence [1]. Permanent magnets made from these alloys are widely
used in many civilian applications including electronics, automotive industry,
radio engineering and automation. e.g. for the small motors in CD and DVD-ROM
drives, zoom lenses, camcorders etc. Improvement of the properties of the
magnets will permit miniaturization of the user end products and therefore
constitutes a significant advance in engineering.
There have been several methods proposed to improve the magnetic properties
such as the powder metallurgy [2], rapid quenching [3], mechanical alloying [4],
hot working [5], sintering, etc. (see Fig. 1 [6]). However, these methods have
their limitations. For instance, the magnets produced by pulverizing the cast
ingot and then sintering did not show sufficient coercivities [7-8]. Moreover,
most of above-mentioned methods led to processing costincrease of permanent
magnets. For solution of this problem in last three decades have been proposed
some new approaches. For instance, in 1978 by Harris et al. [9] at first was
proposed method of hydrogen treatment of hardmagnetic alloys so-called
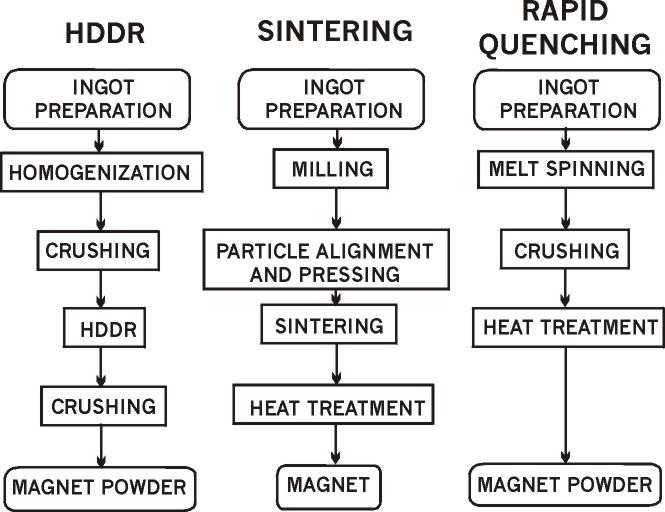
Figure 1.
The main methods permanent magnets production (after [6]).
Hydrogen Decrepitation (HD)
process.Hydrogen Decrepitation of Nd-Fe-B type magnets is a two stage process.
Firstly the hydrogen reacts with the Nd-rich phase at room temperature and then
at temperature increasing up ~ 160oC lead to second stage evolution
in which the hydrogen is absorbed by Nd2Fe14B matrix
phase. In both cases cracking occurs due to differential lattice expansion and
the resulting HD treated alloy is extremely friable. This allows milling times
to be reduced considerable and this is the main factor which reduces the overall
processing cost of permanent magnet manufacture. Thus, using of the HD process
led to increase of permanent magnets coercivity and also led to considerable
decreasing processing cost of permanent magnets on 16-25% [10].
The
recently developed in 1989 by Takeshita and Nakayama [11-12]
HDDR-process
(Hydrogenation- Decomposition-Desorption-Recombination) as a new method of
hydrogen treatment of hard magnetic alloys is very promising from this
viewpoint [13-15]. This HDDR-process provides a new strategy to improve the
properties of permanent magnets via hydrogen-induced phase transformations
in Nd2Fe14B powders. It was found that Nd2Fe14B
magnets produced by HDDR-treatment posses (BH)max more
8-10% than those by mechanical alloyed magnets [16]. Moreover, currently the
HDDR-process is the unique method for production of Nd-Fe-B type anisotropic
powders for permanent magnets (see Fig. 1) [17-19].
1. Principles of HDDR
process and HIDP-transformations
Earlier from the viewpoint of Chemistry the conventional HDDR process in Nd2Fe14B
hard magnetic alloys consists 4 of the following main stages: Hydrogenation,
Decomposition, Desorption, Recombination (see Fig. 2a). As a rule, on first
stage alloy absorbs hydrogen at room temperature (Hydrogenation) and then on
second stage at increasing of temperature up 750-900° C occurs process of
initial Nd2Fe14B alloy decomposition on NdH2,
and Fe2B phases (Decomposition). Subsequent hydrogen evacuation from
decomposed alloy (Desorption) leads to development of recombination process of
decomposed phases into initial Nd2Fe14B phase
(Recombination).
The
main microstructural change during these HIDP-transformations is the conversion
from coarse grains into sub-micron grains (about 0.3-0.5
size, i.e.
comparable with the size of single magnetic domains [7-11]) whereby the magnetic
characteristics are expected to be significantly improved. This hydrogen-vacuum
treatment is perfectly suitable for producing powder samples with extremely high
coercivity, which can be used for producing the Nd-Fe-B base magnets by hot
high-pressure and bonding.
On
the other hand, from the viewpoint of the Solid-State Physics and Material
Science, the HDDR process is based on the following
direct and
reverse
Hydrogen-Induced
Diffusive
Phase (HIDP)
transformations [20-21] (see Fig. 1b).
(1)
Direct HIDP-transformation:
in a hydrogen atmosphere (~ 0.1 MPa) at temperature range of 600-900, the
hydrogen-induced direct phase transformation (decomposition) occurs by the
following chemical reaction [21]:
(1)
(2)
Reverse HIDP-transformation:
the reverse phase transformation (recombination) occurs upon hydrogen evacuation
at ~ 10-2 Torr [21]:
(2)
Moreover, the treatment scheme in the case of HIDP-transformations (see Fig. 2b)
which at first was proposed by Rybalka et. al. [21] is principally different
from conventional HDDR treatment scheme (see Fig. 2a). In this case, the Nd2Fe14B
alloy is heated up in vacuum to high temperatures first (stage I on Fig. 2b),
and then at this constant temperature the reaction chamber is filled with
hydrogen to develop the direct HIDP-transformation (stage
II
on Fig. 2b). Afterwards, when the direct HIDP-transformation is done the
hydrogen is evacuated from chamber, which leads to the development of reverse
HIDP-transformation (stage
III
on Fig. 2b). Finally, when reverse HIDP-transformation development is
finished the Nd2Fe14B alloy powder cooled down to room
temperature in vacuum (stage IV on Fig. 2b).
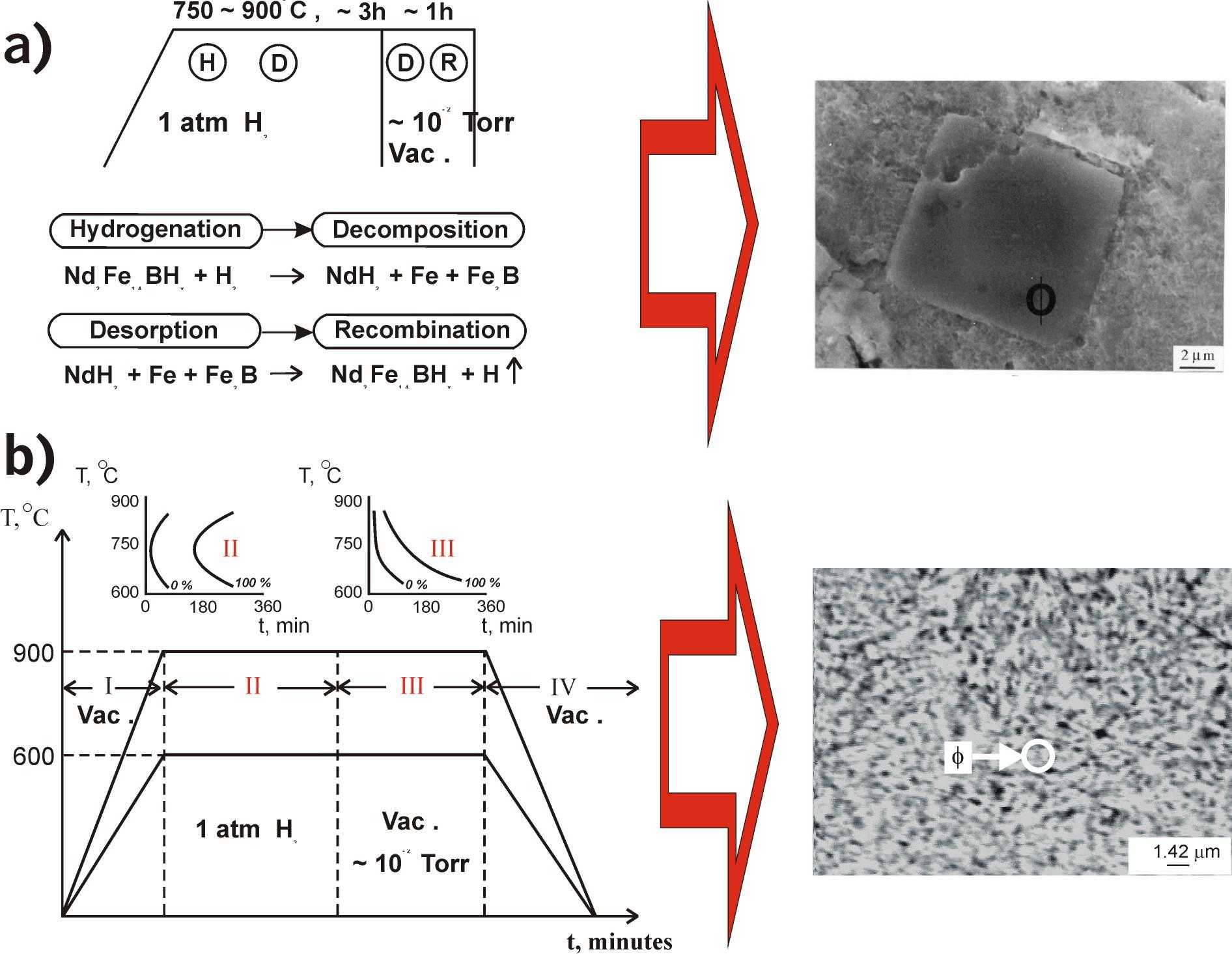
Figure 2. a)
Scheme of conventional HDDR-process (after Takeshita [6]); b) Scheme of
hydrogen treatment based on HIPD-transformations (after Rybalka et al. [21]).
2. Kinetics of the
HIDP-transformation in Nd2Fe14B
type alloys and permanent
magnets properties
It has been established that the magnetic properties
of permanent magnets strongly depend on their microstuctural features [1]. For
instance, the coercive force of permanent magnets is a function of
microstuctural features, such as the average grain size of hard magnetic phase,
grain size distribution, degree of magnetic isolation of hard magnetic phase
etc. [1]. However, the microstuctural features depend on the processing
conditions. For instance, as shown in Fig. 3, the permanent magnets’ coercivity
is a function of such important kinetic parameters as the transformation time
and temperature during the reverse HIDP-transformation in Nd2Fe14B
type alloy [6,22]. This phenomenon of coercivity decrease might be resulting
from the abnormal grains growth processes in case if hydrogen-vacuum treatment
has been carried out after full finishing of HIDP-transformation in Nd2Fe14B
type alloy. If the hydrogen-vacuum treatment in Nd2Fe14B
type alloy carry out without taking into account the kinetic features, such as
the hydrogen pressure, temperature and transformation time according to
conventional HDDR scheme treatment (see Fig. 2a) it can lead to the abnormal
grains growth of hard magnetic phase (Ф
on Fig. 2a) up to tens-hundreds
[23].
Thus, this
kinetic factor
is one of the main factors that lead to coercivity decrease in Nd2Fe14B
type permanent magnets.
Back
to Top
In contrast to the conventional HDDR scheme treatment, if hydrogen-vacuum
treatment is carried out in accordance with the HIDP-transformation scheme based
on T-T-T (Temperature-Transformation-Time) isothermal kinetic diagrams in Nd2Fe14B
type alloy (II
and III
on Fig. 2b) it leads to homogeneous microstructure of Nd2Fe14B
alloy with sub-micron grains of Nd2Fe14B hard magnetic
phase (Ф
on Fig. 2b) and high degree of its magnetic isolation [24,25]. This fact is
prerequisite for improving permanent magnets coercivity [1] made from powder
treated by this way.
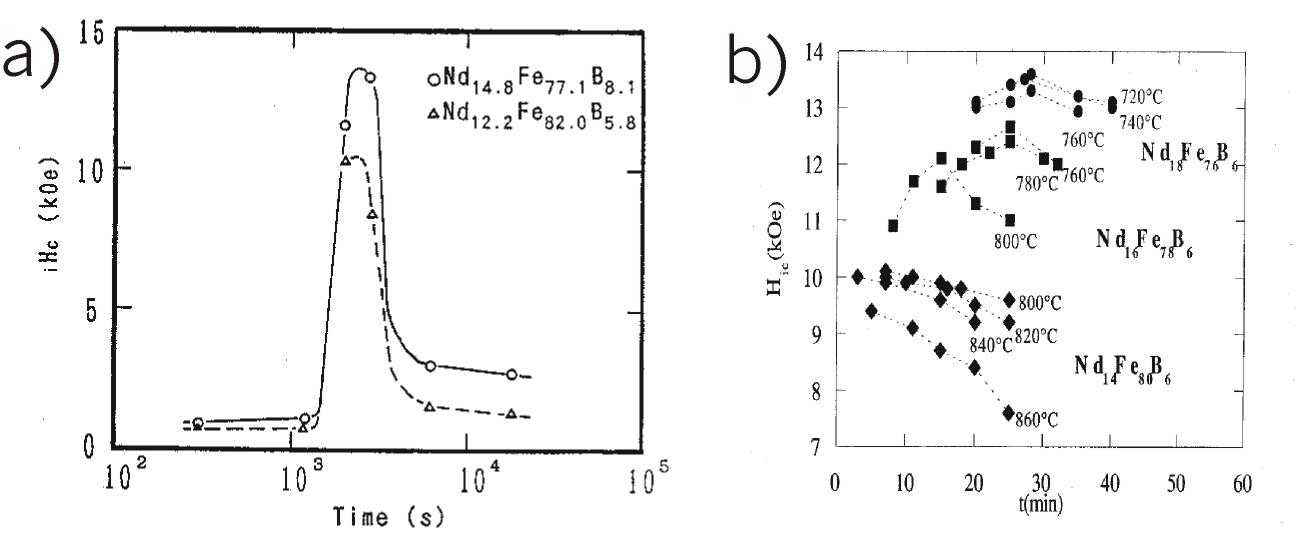
Figure 3.
Permanent magnets coercivity dependence on temperature and transformation time
exposure during reverse HIDP-transformation in Nd2Fe14B
type alloy: a) Takeshita's data [6], b) Liesert's data [22].
So far, researches on the hydrogen-induced phase transformations in Nd2Fe14B
type alloy earlier was limited in the following aspects:
(1) After the classical work by Davenport and
Bain on ferrous alloys [26], it has been well accepted that the isothermal
kinetic diagrams are the primary bases for heat treatment of steels, alloys and
compounds. For the hydrogen-induced phase transformations in Nd2Fe14B
type alloy, however, there is little data on these critical process parameters.
Most of the published hydrogen-vacuum experiments conducted to date have been
carried out empirically without taking into account the kinetic features, such
as the hydrogen pressure, temperature and transformation time and it led to
abnormal growth grains processes and coercivity decrease of permanent magnets.
However, our group has been demonstrated the possibilities of constructing of
the T-T-T isothermal kinetic diagrams hydrogen-induced phase transformations
(HIDP-transformations) in Nd2Fe14B type alloy and also was
shown that kinetics of these type transformations is strongly depend from
temperature treatment and hydrogen pressure [21,27-31]. Moreover, preliminary
experiments based on the T-T-T kinetic diagrams lead to microstructure
homogenization of Nd2Fe14B alloy [32] and submicron grains
of Nd2Fe14B hard magnetic phase (0.3-0.8 )
with high degree of its magnetic isolation [24,25].
(2) There has been very little correlation
between microstructural changes and processing conditions for the
HIDP-transformations.
(3) As a rule, most of the experiments were
carried out on laboratory samples without any real world applications.
3. Conclusions
Thus, we believe that in future a systematic investigation of the
HIDP-transformation
kinetics
and microstructure features
in Nd2Fe14B industrial alloy based on treatment scheme
according Fig. 2b may lead to a
new improved technology of treatment
of Nd2Fe14B hard magnetic alloys, which in future may be
extended on many others classes of hard magnetic materials.
REFERENCES
-
P. Campbell,
Permanent magnet materials and their application, Cambridge University
Press, 1994.
-
M. Sagawa, S.
Fujimura, N. Togawa et al., J. Appl. Phys., 1984, 55, 2083.
-
J.J. Croat, J.F.
Herbst, R.W. Lee et al., J. Appl. Phys., 1984, 55, 2078.
-
L. Schultz, J.
Wecker, E. Hellstern, J. Appl. Phys., 1987, 61, 3583.
-
R.W. Lee,
Appl. Phys. Lett., 1985, 46, 790.
-
T. Takeshita,
J. Alloys Comp., 1995, 231, 51.
-
H.H. Stademaier,
N.C. Lui, Matter. Lett., 1986, 4, 304.
-
C.R. Paik, H.
Mino, M. Okada, H. Homma, IEEE Trans. Mag. Magn., 1987, MAG-23, 2512.
-
Harris I.R.,
McGuiness P.J. Proc. XI Int. Workshop on Rare-Earth Magnets and Their
Applications, Pittsburg, 1990, 29.
-
O.M. Ragg, G.
Keegan et. al., Int. J. Hydrogen Energy, 1997, 22, 333.
-
Takeshita T.,
Nakayama R. Proc. X Int. Workshop on Rare-Earth Magnets and Their
Applications, Kyoto, 1989, 551.
-
Takeshita T.,
Nakayama R. Proc. XI Int. Workshop on Rare-Earth Magnets and Their
Applications, Pittsburg, 1990, 49.
-
X.J. Zhang, P.J.
McGuiness, I.R. Harris, J. Appl. Phys., 1990, 69, 5838.
-
T. Takeshita,
J. Alloys Comp., 1993, 193, 231.
-
O. Gutfleisch,
I.R. Harris, Proc. XV Int. Workshop on Rare-Earth Magnets and Their
Applications, Dresden, 1998, 487.
-
V.N. Verbetsky,
Doctoral thesis, Moscow State University, Moscow, 1998.
-
R. Nakayama, T.
Takeshita, M. Itakura et al., J. Appl. Phys., 1994, 76, 412.
-
T. Takeshita, K.
Morimoto, J. Appl. Phys., 1996, 79, 5040.
-
T. Takeshita, R.
Nakayama, IEEE Trans. J. Magn. Jap., 1993, 8, 692.
-
V.A. Goltsov,
J. Alloys Comp., 1999, 293-295, 844.
-
Rybalka S. B.,
Goltsov V. A., Didus V. A. and Fruchart D. J. Alloys Comp., 2003,
356-357, 386.
-
Liesert S. These
docteur de physique, CNRS, Grenoble, 1998.
-
E. Estevez, J.
Fidler, C. Short, I.R. Harris, J. Phys. D: Appl. Phys, 1996, 29, 951.
-
Rybalka S. B.,
unpublished data.
-
Krayushkina E.Yu., Rybalka
S.B.,
Yurasova V.Yu. Formation of ultrafine nanocrystalline microstructure during
hydrogen-induced reversible phase transformations in Nd2Fe14B
type magnetic alloy // IHISM'15 Junior: Proc.
X International School for young scientists named after A.A. Kyrdumov
'Interaction of Hydrogen isotopes with structural Materials', Sarov, Russia.
— 2016. — P. 108-118.
-
Davenport E.S.,
Bain E.S. AIME Technical Publications , 1930, 90 (348), 117.
-
V.A. Goltsov,
S.B. Rybalka, V.A. Didus, D. Fruchart, Progress in hydrogen treatment of
materials, ed. by V.A. Goltsov, Coral Gables, 2001, 367.
-
Didus V. A.
Rybalka S. B., Fruchart D. and Goltsov V. A. J. Alloys Comp., 2003,
356-357, 390.
-
V.A. Goltsov,
S.B. Rybalka, A.F. Volkov, Int. J. Hydrogen Energy, 1999, 24, 913.
-
V.A. Goltsov,
S.B. Rybalka, A.F. Volkov et al., Metal Physics and Advanced Technologies,
1999, 21, 22.
-
V.A. Goltsov,
S.B. Rybalka, A.F Volkov et al., The Physics of Metals and Metallography,
2000, 89, 363.
-
A.A. Didus,
S.B.Rybalka, V.A. Didus, A.F.Volkov,
Bull. DonGASA,
2001, 3, 15.
Back
to Top
Back
to Main page
|